In the ever-evolving landscape of industrial automation and electromechanical systems, the demand for precise, durable, and adaptable testing equipment has never been greater. At the intersection of innovation and reliability lie hysteresis brakes, hysteresis dynamometers, hysteresis clutches, and integrated motor test systems—technologies that redefine performance benchmarking across industries. This article explores how these solutions empower engineers to push boundaries while maintaining operational excellence.
THE SCIENCE BEHYSTERESIS TECHNOLOGY
Hysteresis devices derive their name from the magnetic hysteresis phenomenon, where magnetic materials exhibit lagging responses to applied magnetic fields. This principle enables non-contact torque control, making hysteresis-based equipment uniquely suited for applications requiring smooth operation, minimal wear, and exceptional repeatability. Unlike Torque testing for stepper motors -based systems, hysteresis devices eliminate mechanical contact between components, dramatically reducing maintenance needs and extending service life.
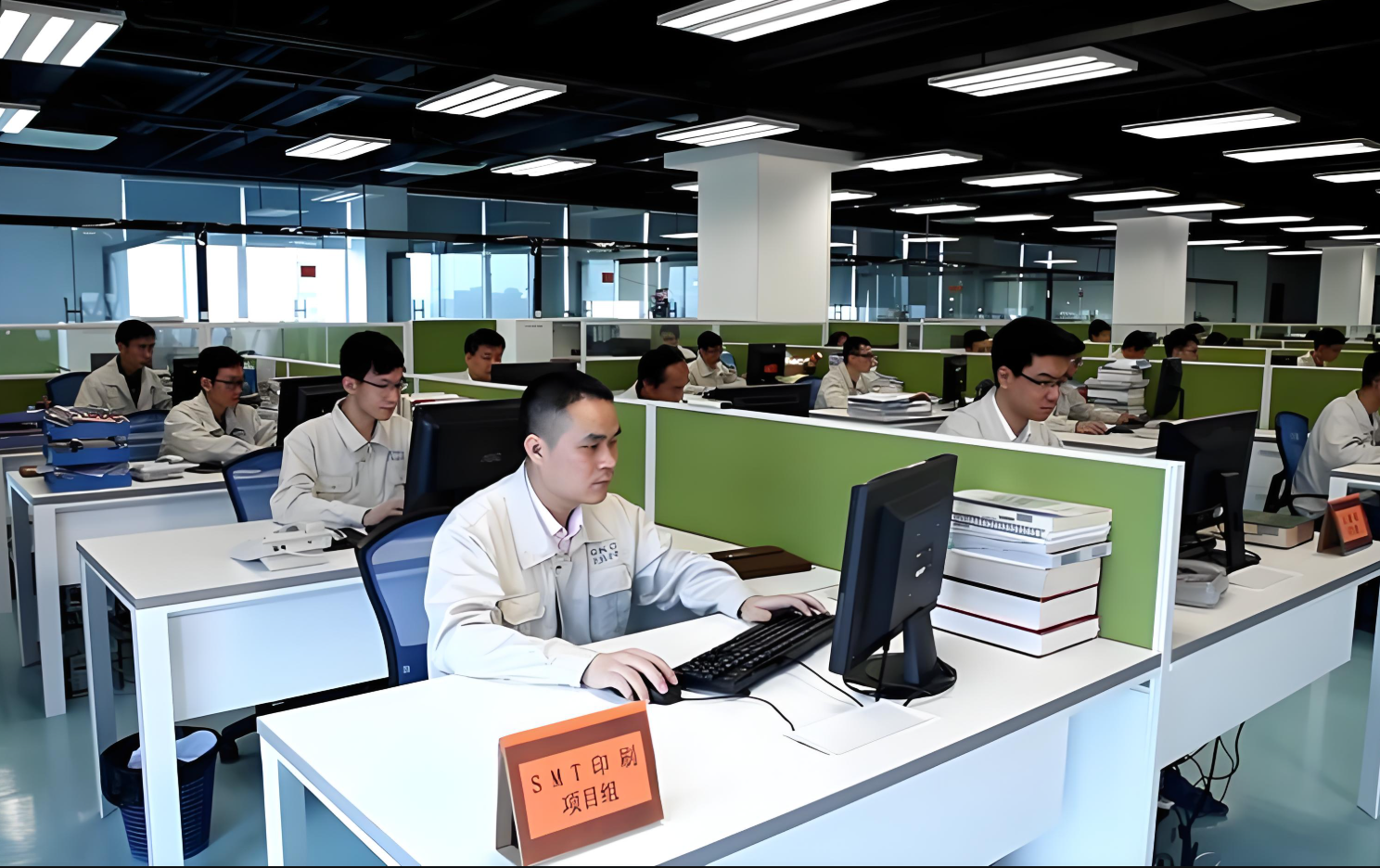
HYSTERESIS BRAKES: THE SILENT WORKHORSES
Modern hysteresis brakes excel in scenarios demanding precise load simulation and dynamic braking. Their ability to generate torque proportional to excitation current makes them indispensable for:
- Material tension control in web processing (films, textiles, paper)
- Precision positioning systems in robotics and aerospace
- Fatigue testing of components under controlled resistive forces
A key advantage lies in their torque linearity across wide speed ranges, including zero RPM. This allows engineers to simulate real-world inertial loads with unprecedented accuracy, whether testing micro-motors for medical devices or high-torque industrial drives.
HYSTERESIS DYNAMOMETERS: MEASURING WHAT OTHERS MISS
When paired with advanced sensor arrays, hysteresis dynamometers become the ultimate diagnostic tool for motor and powertrain validation. Their unique capabilities include:
1. Bidirectional testing without mechanical reconfiguration
2. Instantaneous torque response for capturing transient behaviors
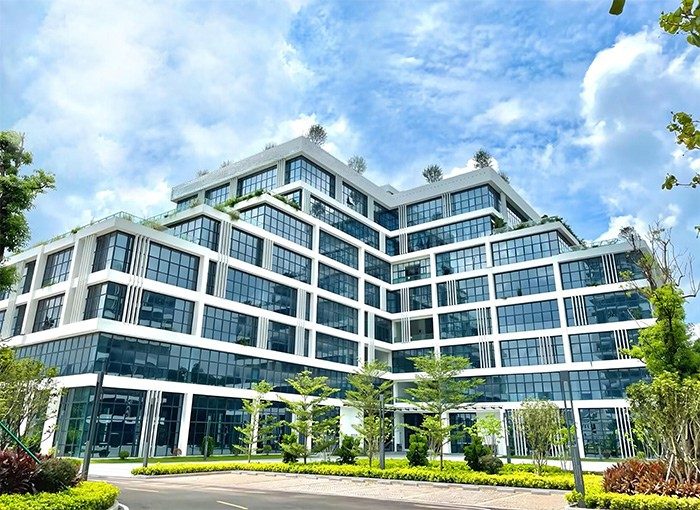
3. Energy recovery features that reduce testing facility power consumption
These dynamometers shine in automotive R\u0026D labs testing EV traction motors, where they precisely measure efficiency maps across thousands of operating points. Recent advancements incorporate real-time thermal modeling, allowing predictive cooling adjustments that prevent system derating during prolonged test cycles.
HYSTERESIS CLUTCHES: PRECISION IN MOTION CONTROL
Bridging the gap between mechanical and electronic control systems, hysteresis clutches enable:
- Shock-free torque transmission in packaging machinery
- Torsional vibration damping in turbine generator sets
- Slip-controlled power transmission for safety-critical systems
The absence of wear particles makes these clutches particularly valuable in cleanroom environments like semiconductor manufacturing. Modern designs integrate IoT-ready sensors that monitor coil temperatures and torque output, enabling predictive maintenance strategies.
INTEGRATED MOTOR TEST SYSTEMS: WHERE COMPONENTS BECOME SOLUTIONS
Contemporary motor test equipment transcends mere data acquisition. Comprehensive test systems now combine hysteresis loading devices with:
- Multi-axis power analyzers
- Environmental chambers simulating extreme temperatures
- AI-driven anomaly detection algorithms
Aerospace applications demonstrate this integration perfectly. Testing an aircraft actuation motor now involves not just torque-speed validation, but simultaneous monitoring of:
- Harmonic distortion under variable voltage conditions
- EMI/RFI emissions at different altitudes
- Lubricant performance in vacuum simulations
Such systems employ adaptive load profiles that automatically adjust based on real-time motor responses, compressing test durations while improving data richness.
THE EVOLUTION OF TEST AUTOMATION
Modern motor test systems leverage digital twin technology to create virtual proving grounds. Engineers can:
- Replicate field failure scenarios in controlled lab environments
- Perform accelerated life testing using AI-generated stress profiles
- Validate control algorithms against digital prototypes before physical builds
This paradigm shift reduces development cycles for emerging technologies like axial flux motors and superconducting drives. Automated report generation tools now translate raw data into compliance documentation for international standards (IEC, UL, SAE), significantly streamlining certification processes.
SUSTAINABILITY THROUGH INNOVATION
Next-generation hysteresis systems address environmental concerns through:
- Regenerative power systems that feed energy back to the grid
- Rare-earth-free magnetic circuit designs
- Compact liquid cooling systems reducing facility water usage
A notable case study involves a European wind turbine manufacturer that reduced prototype validation energy consumption by 40% using hybrid hysteresis-eddy current dynamometers with power recovery capabilities.
CUSTOMIZATION: THE NEW INDUSTRY STANDARD
Recognizing that no two testing challenges are identical, leading manufacturers now offer modular platforms. Users can configure systems with:
- Interchangeable hysteresis and powder brake modules
- Scalable DAQ resolutions from 16-bit to 24-bit
- Customizable software interfaces supporting Python scripting and MATLAB integration
This flexibility proves crucial for R\u0026D teams working on cutting-edge applications like artificial muscle actuators or magnetorheological fluid-based systems.
THE HUMAN FACTOR IN TESTING TECHNOLOGY
Despite increasing automation, intuitive human-machine interfaces remain crucial. Modern control systems feature:
- Haptic feedback joysticks for precise manual override
- Augmented reality troubleshooting guides
- Voice-controlled test sequence initiation
These ergonomic advancements reduce operator fatigue during prolonged testing sessions while maintaining critical human oversight in complex validation processes.
FUTURE HORIZONS
Emerging trends point toward:
- Quantum-sensitive torque measurement techniques
- Self-calibrating hysteresis systems using embedded reference loads
- Neuromorphic computing architectures for real-time system optimization
Ongoing research in room-temperature superconducting materials promises to revolutionize hysteresis device efficiency, potentially doubling torque density while eliminating cooling requirements.
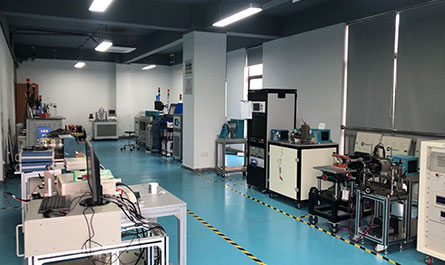
From the micro-scale precision required in watch motor assembly to the megawatt-level testing of ship propulsion systems, hysteresis-based technologies and advanced motor test equipment continue to redefine the boundaries of electromechanical validation. As industries push toward higher efficiencies and smarter automation, these systems stand as both enablers and benchmarks of technological progress—silent guardians ensuring that every revolution counts, every watt is accounted for, and every innovation undergoes the scrutiny it deserves before shaping our engineered world.